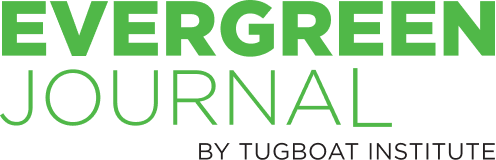
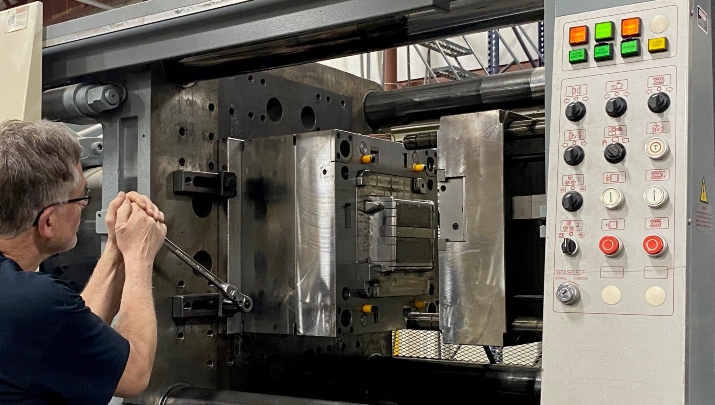
Onshoring as an Evergreen Strategy
- Jonathan Deutsch
- DEMA Engineering Company
As businesses evolve and market conditions change, we as leaders adapt our strategies, experiment with new initiatives, build and rebuild our structures to maximize opportunities. In recent years, the shifts in the market have been dramatic and have caused us here at DEMA Engineering Company, like so many of you, to adapt and even roll back some initiatives that had seemed so right just a few years earlier. Some of these reversals have caused us to learn powerful lessons about what is right for an Evergreen® company in the long term, regardless of market conditions. Our journey to and from offshoring is a great example of this.
For us, the move toward offshoring started all the way back in the 1980s, when we started exploring some partnerships with companies who made injection molding parts in Taiwan. The reasons were clear; the cost of steel to make the tools and the cost of labor–and therefore the parts themselves–were far less than in the US. It was quickly becoming the case that making the tools necessary for running the injection molding parts, even more than making the parts themselves, was so expensive in the US that very few companies were doing it anymore. We found we had no choice, so we made the smart and obvious move.
This shift was happening on a huge scale, in manufacturing as well as a great many other industries. We chose to work with partners in Taiwan, with brokers who managed our relationships, instead of in China because we found that we were able to establish better relationships and communicate more easily, even though costs were higher there than in mainland China.
All of this became easier, even in China, in the 1990s. With the rise of email, communication became easier and more barriers to doing business in Asia fell. We were able to start doing direct sourcing, in Taiwan especially, and bypass the brokers, thereby reducing our costs even further. I don’t mean to minimize the role of China in all of this; we did and still do buy parts from China. It’s difficult to avoid. But it was not our primary market. For the last 20-25 years, our partnerships with suppliers in Taiwan became the core of our business for bringing in injection molded parts.
For obvious reasons, everything shifted suddenly and almost entirely in 2020. The biggest problem for us, as for so many, was the cost of freight, which had skyrocketed overnight. We went from a 40-foot shipping container costing $3,500 to costing over $28,000. You can imagine how much was dropping straight from the bottom line. Between the freight cost that had skyrocketed and the strikes in the ports, labor shortages, unreliable delivery timeframes, and all the mess we saw around covid, it was no longer workable and was imposing extremely challenging and unpredictable circumstances on our business. Add the price increases worldwide, geo-political challenges, tariffs– the uncertainty became too much. This is what pushed us to start to imagine a change.
As we started to imagine ways to mitigate this series of issues, we faced several challenges. One of the most significant grew out of the fact that, over the last 30 years, because of the situation I have described, production of certain products and processes, especially in injection molding, vacated the US almost entirely. For the molded parts, which were also hard to find, we made the decision to start molding them in the US ourselves, even though the cost was higher. We have done this in several ways.
We are able to source some of the parts right here in Missouri. We have a number of small partners here that we work with locally and we are growing that network. It’s not cheap, but we are saving on freight, and we have regained reliability when it comes to delivery times, which is huge for us. We also acquired a subsidiary company in Pennsylvania in 2006 that does injection molding, and since 2020, we have invested in that too, to help increase production. We are basically buying those parts from ourselves, so that helps mitigate the higher cost there, as we are supporting our own business. When we used to start a new project, we would go to Taiwan to get it going. Now, we are starting our new projects at home. We are carrying less inventory and we are being more strategic about the parts we do still ship from Taiwan, being conscious of the size and nest-ability, so we are shipping containers with less empty space.
All of this has helped us reduce our lead times, reduce the amount of money tied up in inventory, and regain consistency of both pricing and delivery of our products. Eliminating the wild uncertainty we were experiencing has been extremely important. But it’s a process; it will take time to truly complete this shift.
Today, we have brought back about 20% of the product we had been sourcing overseas. This number is going to continue to grow. Especially for new projects, we are bringing the tools themselves that make the parts back onshore, and then we can start making the parts here, in Missouri or in Pennsylvania. For the last three big projects we’ve done, we’ve been able to onshore most of the parts.
We regularly share this onshoring strategy with our largest customers and they are very supportive of these efforts. They also understand the benefits of reducing lead times and gaining predictability. Our business will never be entirely domestically sourced, but more and more is moving back home, and we feel very good about our decision.
I keep the Evergreen 7Ps® principles right here by my desk and I have been thinking about Paced Growth and Private in particular a lot recently. We wouldn’t be able to do this if we weren’t Private; it will take time for the investments we are making, especially in our Pennsylvania company, to yield results and return us to strong profitability. If we had a short-term mentality, we would have to follow the lower prices, like many of our competitors are doing. But we are diversifying and integrating at the same time, which will, in the end, make us a stronger company, better prepared to weather whatever the next 100 years have in store for us.
More Articles and Videos
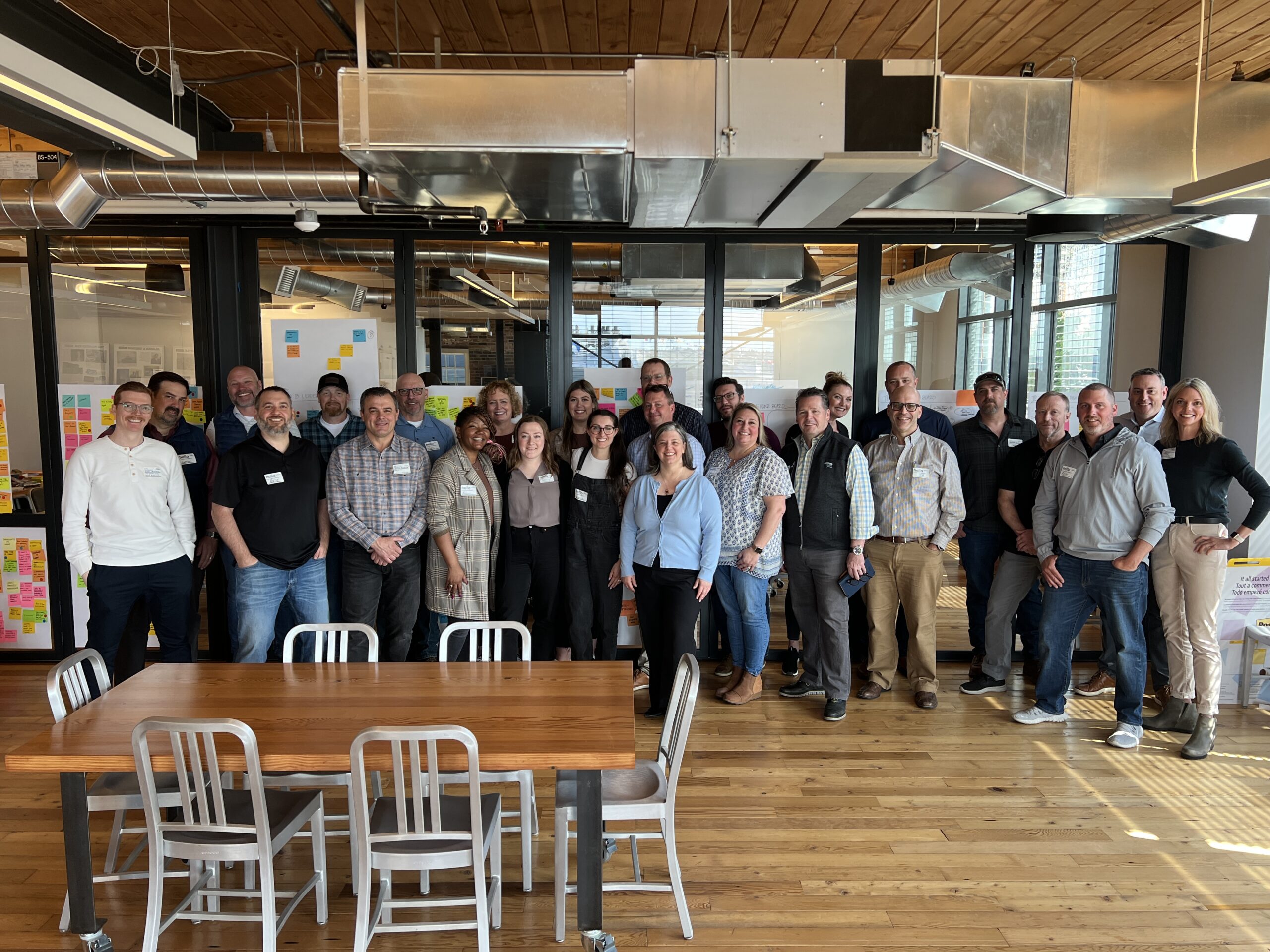
Creating an Employee Value Proposition Straight from the Source
- Bart Ricketts
- Lease Crutcher Lewis
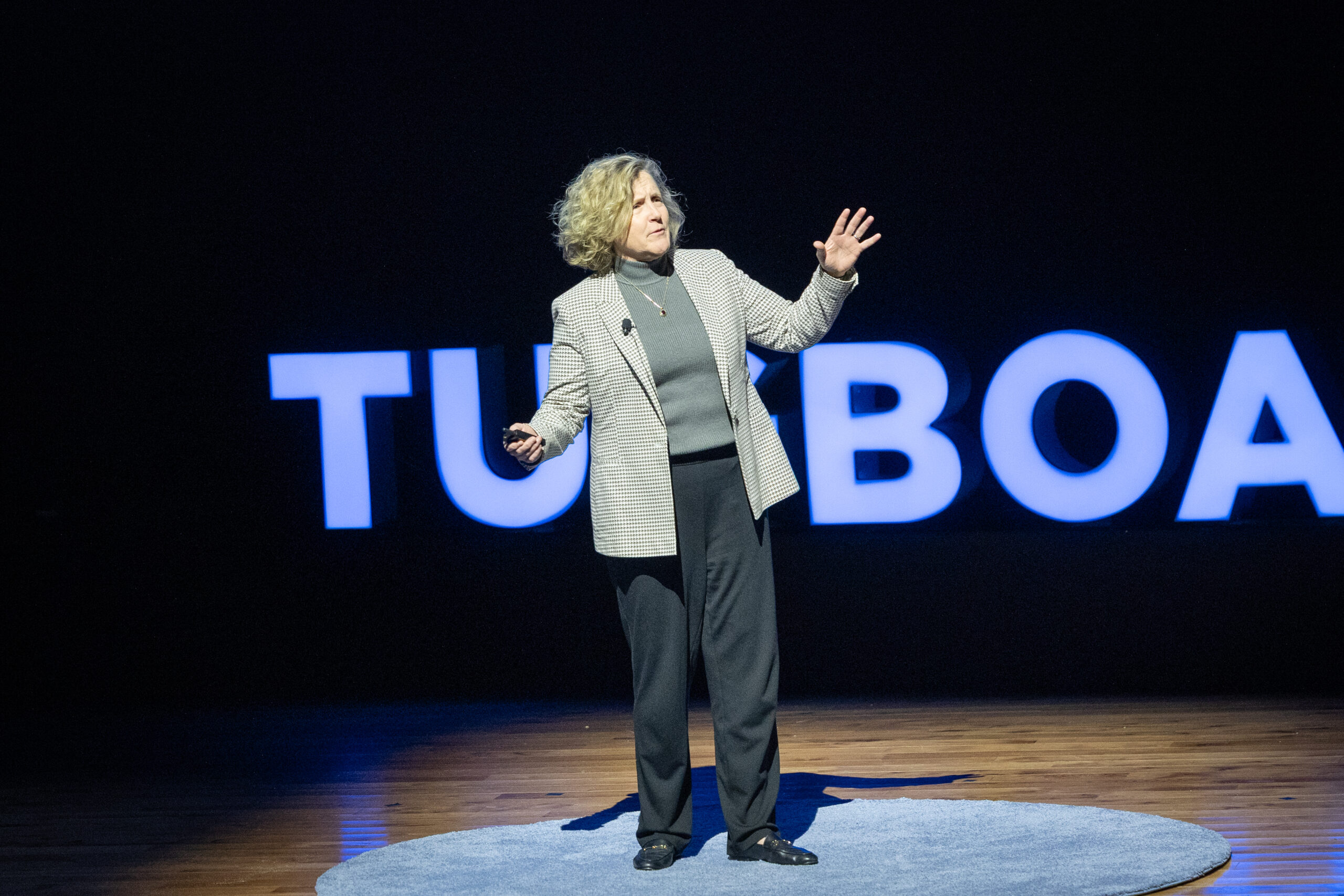
Both/And Thinking: Harnessing the Positive Potential of Tensions
- Marianne Lewis
- Carl L. Linder College of Business, University of Cincinnati
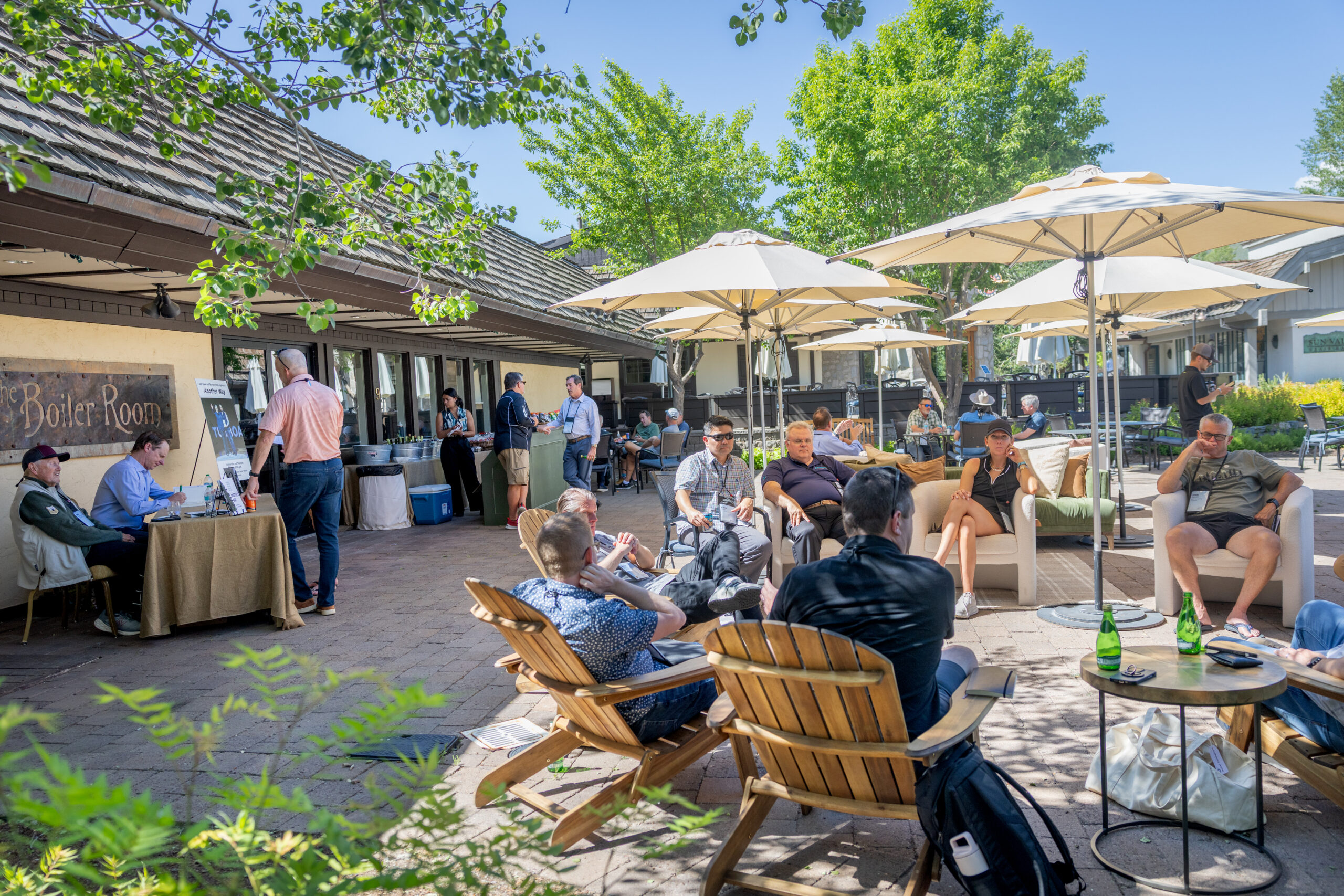
Leading Through Uncertainty – Tugboat Institute® Summit 2025
- Jackie Hawkins
- Tugboat Institute
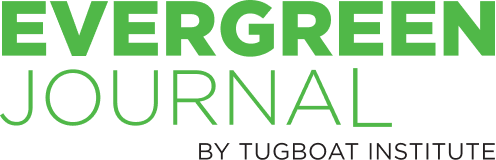
Get Evergreen insight and wisdom delivered to your inbox every week
By signing up, you understand and agree that we will store, process and manage your personal information according to our Privacy Policy